Welcome to My Blog!
Before we dive into the content, I’d love for you to join me on my social media platforms where I share more insights, engage with the community, and post updates. Here’s how you can connect with me:
Facebook: https://www.facebook.com/profile.php?id=100072217509763
LinkedIn: https://www.linkedin.com/company/74949059/admin/dashboard/
YouTube:www.youtube.com/@tractormanufacturer-lc5qz,www.youtube.com/@excavatormanufacturers-sn9hk
TikTok: www.tiktok.com/@tractormanufacturer, www.tiktok.com/@excavatormanufacturers
Now, let’s get started on our journey together. I hope you find the content here insightful, engaging, and valuable.
Table of Contents
Introduction
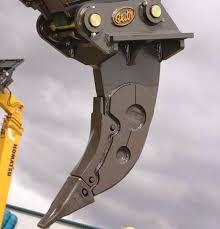
An excavator ripper machine is a heavy-duty attachment designed to equip excavators with powerful ripping capabilities. Primarily used for breaking up hard materials such as rock, frozen ground, and paved surfaces, ripper machines for excavators are indispensable in construction, mining, and land clearing operations. This comprehensive guide aims to provide in-depth information about excavator ripper machines, including their types, applications, benefits, selection criteria, and maintenance tips. By understanding the intricacies of ripper machine for excavator technology, you can optimize your excavation projects and achieve maximum productivity.
Understanding Excavator Ripper Machines
What is an Excavator Ripper Machine?
An excavator ripper machine is a specialized attachment, typically a single or double shank, that is mounted on the end of an excavator’s arm. The ripper’s shank is equipped with a hardened tip or tooth designed to penetrate and fracture hard materials. This powerful tool enables excavators to efficiently break through tough obstacles, significantly increasing their versatility and productivity.
How Does an Excavator Ripper Machine Work?
The ripper machine for excavator is lowered into the material to be broken up. The excavator’s hydraulic system applies downward force, driving the shank into the material. As the shank penetrates, the tip or tooth fractures the material, allowing it to be easily removed. The process involves a combination of sheer force and impact, enabling the ripper machine to handle a wide range of materials, from soft soil to solid rock.
Types of Excavator Ripper Machines
Excavator ripper machines come in various types, each designed for specific applications and ground conditions. Understanding the different types of ripper machines for excavators is essential for selecting the right tool for your job.
- Single Shank Ripper Machines: Suitable for a wide range of applications, single shank ripper machines are versatile and easy to maneuver. They are commonly used for general excavation, trenching, and breaking up moderately hard materials.
- Double Shank Ripper Machines: Offering increased ripping force, double shank ripper machines for excavators are ideal for breaking up extremely hard materials such as solid rock and heavily compacted soil. They are commonly used in mining, quarrying, and heavy-duty construction projects.
- Hydraulic Hammer Ripper Machines: These ripper machines combine the power of a hydraulic hammer with the penetrating force of a ripper, making them highly effective for breaking up concrete, asphalt, and other reinforced materials. They are often used in demolition and road repair projects.
Benefits of Using an Excavator Ripper Machine
- Increased Efficiency: Ripper machines for excavators significantly increase productivity by breaking up hard materials quickly and efficiently, reducing the time and effort required for excavation and land clearing.
- Versatility: Ripper machines can be used for a wide range of applications, making them a valuable asset to any construction or mining operation. They can handle various materials and ground conditions, adapting to different project requirements.
- Cost-Effective: While the initial investment in a ripper machine may be significant, it can save money in the long run by reducing the need for other equipment and labor. Ripper machines for excavators can significantly reduce project timelines and labor costs, leading to overall cost savings.
- Reduced Vibration: Compared to hammer attachments, ripper machines generate less vibration, reducing wear on the excavator and discomfort for the operator. Lower vibration levels contribute to a more comfortable and efficient working environment.
Choosing the Right Excavator Ripper Machine
When selecting an excavator ripper machine, several factors must be considered to ensure optimal performance and efficiency:
- Excavator Size: The ripper machine must be compatible with the size and capacity of your excavator to avoid overloading the machine and compromising safety.
- Ground Conditions: The type of material to be ripped will determine the required shank size and tooth configuration. For softer materials, a smaller shank may suffice, while harder materials may require a larger shank and stronger teeth.
- Application: The specific application will influence the choice of ripper machine type. For example, a single shank ripper machine may be suitable for general excavation, while a double shank ripper machine may be necessary for breaking up solid rock.
Key Specifications of Different Ripper Machine Types
Ripper Machine Type | Shank Configuration | Typical Applications | Advantages | Disadvantages |
---|---|---|---|---|
Single Shank Ripper Machine | One shank | General excavation, trenching, breaking up moderately hard materials | Versatile, easy to maneuver | Lower ripping force compared to double shank |
Double Shank Ripper Machine | Two shanks | Breaking up extremely hard materials such as solid rock and heavily compacted soil | High ripping force, increased productivity | Less maneuverable than single shank |
Hydraulic Hammer Ripper Machine | Combination of hammer and ripper | Breaking up concrete, asphalt, and other reinforced materials | High impact force, versatility | Higher maintenance costs, increased noise and vibration |
Maintenance and Safety

Proper maintenance is essential to ensure the long life and optimal performance of your excavator ripper machine. Regular inspections, lubrication, and sharpening of the teeth are crucial to prevent premature wear and tear. Additionally, operators should always adhere to safety guidelines when using an excavator ripper machine, including wearing appropriate protective gear and following safe operating procedures.
Conclusion
Excavator ripper machines are powerful tools that can significantly enhance the efficiency and productivity of construction and mining operations. By understanding the different types of ripper machines for excavators, their benefits, and the factors to consider when selecting one, you can make an informed decision to improve your operations.
FAQ
What is the difference between a ripper machine and a bucket?
A ripper machine is designed specifically for breaking up hard materials, while a bucket is used for digging and moving materials.
How do I choose the right ripper tooth for my excavator ripper machine?
The type of material being ripped, the hardness of the material, and the frequency of use will influence the choice of ripper tooth. Consult with the manufacturer or a knowledgeable equipment dealer for specific recommendations.
What is the lifespan of an excavator ripper machine?
The lifespan of an excavator ripper machine can vary depending on factors such as the type of material being ripped, the frequency of use, and the quality of maintenance. With proper care and maintenance, a ripper machine can last for many years.
Can I use a ripper machine to break up rocks?
Yes, ripper machines are specifically designed to break up rocks. The type of ripper machine and the size of the rocks will determine the effectiveness of the process.
Is it safe to operate an excavator with a ripper machine?
Yes, it is safe to operate an excavator with a ripper machine as long as the operator is properly trained and follows safety guidelines. Always wear appropriate protective gear and be aware of your surroundings.