Welkom op mijn blog!
Ik ben blij dat je er bent! Voordat we in de inhoud duiken, zou ik het leuk vinden als je me volgt op mijn social media platforms. Hier deel ik extra inzichten, ga ik de dialoog aan met een geweldige community en houd ik je op de hoogte van het laatste nieuws. Dit is hoe je op de hoogte kunt blijven:
Facebook: Connect met mij op Facebook
LinkedIn: Volg me op LinkedIn
▶️ YouTube: Kanaal trekkerfabrikant,Graafmachine fabrikanten kanaal
TikTok: Tractor Fabrikant,Graafmachine Fabrikant
Laten we nu samen aan deze reis beginnen! Ik hoop dat je de inhoud hier inzichtelijk, boeiend en vooral waardevol vindt. Laten we ontdekken, leren en groeien!
Inhoudsopgave
Inleiding
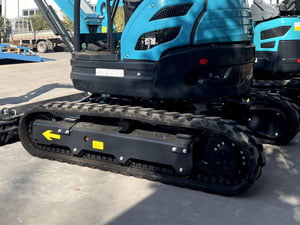
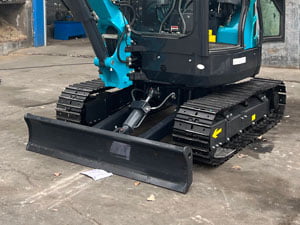
Minigraafmachine tracks play a crucial role in ensuring stability, traction, and performance on the job site. Over time, wear and tear compromise the effectiveness of tracks, leading to reduced productivity, increased maintenance costs, and safety risks. Knowing when to upgrade your mini excavator tracks can save you significant downtime and expenses. In this comprehensive guide, we’ll discuss five clear signs that your mini excavator tracks may be due for an upgrade, and how modern track options can restore performance and reliability.
By proactively monitoring track condition and addressing issues early, equipment owners can optimize machine availability, reduce operating costs, and extend the lifespan of undercarriage components. Whether you manage a fleet of mini excavators or are a contractor relying on a single machine, understanding these maintenance indicators will help you plan replacements effectively and avoid unexpected failures.
Sign 1. Excessive Track Wear Patterns on Minigraafmachine Tracks
One of the first indicators that you should consider upgrading mini excavator tracks is when the metal links, pads, or bushings exhibit uneven or excessive wear. Visual inspection of the undercarriage can reveal serious problems:
1.Identifying Wear on Track Pads and Shoes
Track pads and shoes form the direct interface with the ground. Over time, the pad tread wears down, reducing grip on soft or uneven terrain. Look for:
- Smoothing or rounding of pad edges
- Exposed metal surfaces where rubber or casting has worn away
- Cracks near bolt holes or weld joints
These symptoms indicate that traction is compromised and slippage under load may occur. Continued operation on worn pads can accelerate stress on sprockets and idlers.
2.Measuring Link Wear and Bushing Play
Track links and bushings determine track tension and alignment. Measure the distance between links and inspect side clearance:
- Excessive side-to-side play suggests bushing wear
- Increased pitch (distance between links) reduces mesh with sprockets
Typically, when bushing wear exceeds 15% of original tolerances, it is time to upgrade your minigraafmachine tracks to avoid derailment and uneven loading on the chassis.
3.Impact of Wear on Undercarriage Components
Worn tracks transfer irregular forces to rollers, idlers, and sprockets. Symptoms include:
- Irregular roller wear patterns
- Sprocket tooth chipping or hooking
- Increased track chain tension requirements
These secondary failures can rapidly escalate maintenance costs. Proactive track replacement prevents collateral damage to expensive undercarriage parts.
Sign 2. Frequent Track Tension Adjustments Needed with Mini Excavator Tracks
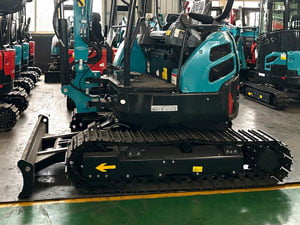
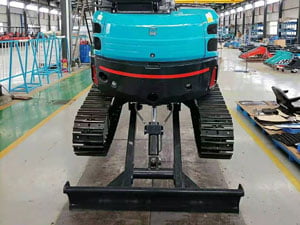
Maintaining proper track tension is vital for efficient machine operation. If you find yourself constantly adjusting tension bolts, it may signal that your minigraafmachine tracks are loosening prematurely.
1.Causes of Track Slack
Factors contributing to slack include:
- Worn bushings increasing chain elongation
- Damaged tension piston seals causing fluid leaks in hydraulic tensioners
- Foundation frame wear allowing idler displacement
Track slack leads to accelerated wear, higher fuel consumption due to inefficiency, and potential derailment during high-speed travel modes.
2.Monitoring and Adjusting Track Tension
A best practice is to check tension daily or after substantial operating hours. Measure deflection under standard load:
- Deflection greater than specified mm/inches indicates need for tensioning
- Inspect hydraulic tensioner rods for fluid leaks
When adjustments exceed factory recommendations more than twice per month, upgrading to modern tracks with improved bushing materials or alternative tensioning systems can reduce maintenance demands.
Sign 3. Unusual Noise and Vibration from Mini Excavator Tracks
Audible or tactile feedback from the undercarriage can warn of track issues before they become catastrophic.
1.Diagnosing Track-Related Noise
Listen for:
- Grinding or metal-on-metal scraping indicative of misaligned links
- Clicking or clunking as individual segments disengage and re-engage
- Squealing reported when seals fail and allow debris ingress
These sounds suggest degrading track integrity and contamination in bushings or seals.
2.Vibration Effects on Operator Comfort and Component Life
Excessive vibration causes:
- Operator fatigue reducing productivity
- Accelerated hydraulic pump wear due to pulsating loads
- Loosening of fasteners and auxiliary equipment
Replacing worn tracks with models featuring precision-machined rollers and sealed bushings can dramatically reduce vibration and noise levels.
Sign 4. Slippage and Traction Loss on Mini Excavator Tracks
When your minigraafmachine struggles to climb slopes or moves erratically on loose ground, it’s a clear sign that track traction has diminished.
1.Factors Causing Traction Loss
Key contributors include:
- Worn pad surface pattern reducing soil engagement
- Increased track tension reducing contact area
- Mud and debris buildup in track segments
Inspect and clean tracks regularly, but persistent slippage even on cleaned tracks indicates inadequate pad life.
2.Impact of Poor Traction on Job Performance
Consequences of traction loss:
- Slower cycle times on grading or excavation
- Increased fuel consumption as engines work harder
- Higher risk of equipment slide or tip-over on inclines
Upgrading to specialized rubber or steel pad designs optimized for muddy, rocky, or inclined terrain can restore grip.
Sign 5. Cracking and Structural Fatigue in Minigraafmachine Tracks
Cracks in track components are the most severe warning sign and demand immediate attention.
1.Common Crack Locations
Inspect for:
- Hairline cracks on link plates near pin holes
- Fractures on mounting brackets where pads bolt on
- Cracks propagating along the rubber-metal interface on hybrid tracks
Structural fatigue often begins as micro-cracks under high stress cycles and grows if left unchecked.
2.Consequences of Structural Failure
A single crack can lead to:
- Sudden track breakage and machine immobilization
- Risk of injury from flying debris if track link fails under tension
- Extensive damage to rollers and idlers from derailment
Immediate replacement of cracked tracks is non-negotiable for safety and continuity of operations.
Table of Minigraafmachine Tracks Upgrade Indicators
Sign | Symptoms | Inspection Method | Recommended Action |
---|---|---|---|
Excessive Track Wear | Smooth pads, worn bushings | Visual & caliper measure | Upgrade to new track assemblies |
Frequent Tension Adjustments | Repeated bolt tightening | Daily tension check | Install tracks with improved bushings |
Unusual Noise & Vibration | Grinding, clunking, operator discomfort | Sound & vibration meter | Replace with sealed bushing tracks |
Slippage & Traction Loss | Difficulty climbing, erratic movement | Load test on incline | Switch to deep-lug or hybrid tracks |
Cracking & Structural Fatigue | Visible cracks near pin holes | Dye penetrant inspection | Immediate full track replacement |
Additional Considerations When Upgrading Minigraafmachine Tracks
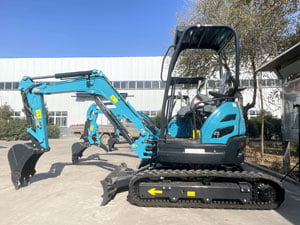
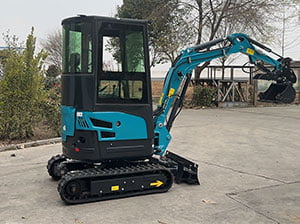
Beyond the five primary signs, several other factors influence track selection and upgrade success.
Material Choice: Steel vs Rubber Tracks
Understanding the trade-offs:
- Steel tracks offer durability on rocky terrain but increase ground damage.
- Rubber tracks are gentler on asphalt and soft soils but wear faster under sharp debris.
Track Width and Ground Pressure
Wider minigraafmachine tracks reduce ground pressure, minimizing soil compaction and improving floatation in soft soils. Select track width based on jobsite conditions.
Maintenance and Lubrication Requirements
New track technologies feature sealed and lubricated bushings, reducing daily greasing intervals. Factor these savings into total cost of ownership calculations.
Conclusie
Recognizing the five signs—excessive wear, frequent tension adjustments, noise and vibration, traction loss, and cracking—allows you to plan timely upgrades to minigraafmachine tracks. Replacing worn undercarriage components prevents costly downtime, enhances safety, and improves operational efficiency.
When choosing new tracks, weigh factors such as material, width, and maintenance needs against your specific application requirements. Investing in high-quality tracks tailored to your environment ensures long-term performance and savings.
FAQ
What is the average lifespan of minigraafmachine tracks?
Under normal conditions, steel tracks last 1,200–1,500 hours, while rubber tracks last 900–1,200 hours, depending on terrain and maintenance practices.
How often should I inspect my minigraafmachine tracks?
Perform daily visual inspections and a detailed assessment every 100 operating hours, focusing on wear patterns and tension.
Can I replace only individual links or pads instead of full track assemblies?
Some track systems allow link or pad replacement, but mismatched components can cause uneven wear. Full track replacement is recommended for best performance.
Are hybrid tracks a good compromise?
Hybrid tracks combine steel inner links with rubber pads, offering improved traction and reduced ground damage. They suit mixed-terrain operations.
How do I choose the right track width?
Select width based on ground conditions: narrow tracks for firm surfaces and wider tracks for soft or muddy terrains to reduce ground pressure.
What maintenance adds life to mini excavator tracks?
Regular cleaning, proper tensioning, daily inspection, and greasing of sealed bushings (if applicable) extend track life significantly.
Do aftermarket tracks perform as well as OEM?
Quality aftermarket brands can match OEM performance if sourced from reputable suppliers, though warranty terms may vary. Always verify specifications and material grades.
How much downtime does a track upgrade require?
A full undercarriage change typically takes 4–8 hours, depending on machine model and workshop facilities.
Can worn tracks affect fuel efficiency?
Yes, worn tracks increase rolling resistance, causing up to 10% higher fuel consumption. Upgraded tracks restore efficiency.
Is professional installation necessary?
Professional installation ensures correct tensioning and alignment, reducing the risk of premature wear and improving safety during replacement.