Welkom op mijn blog!
Ik ben blij dat je er bent! Voordat we in de inhoud duiken, zou ik het leuk vinden als je me volgt op mijn social media platforms. Hier deel ik extra inzichten, ga ik de dialoog aan met een geweldige community en houd ik je op de hoogte van het laatste nieuws. Dit is hoe je op de hoogte kunt blijven:
Facebook: Connect met mij op Facebook
LinkedIn: Volg me op LinkedIn
▶️ YouTube: Kanaal trekkerfabrikant,Graafmachine fabrikanten kanaal
TikTok: Tractor Fabrikant,Graafmachine Fabrikant
Laten we nu samen aan deze reis beginnen! Ik hoop dat je de inhoud hier inzichtelijk, boeiend en vooral waardevol vindt. Laten we ontdekken, leren en groeien!
Inhoudsopgave
Inleiding
Minigraafmachine digging is an essential task across many construction, landscaping, and utility projects. Compact, powerful, and adaptable, mini excavators can perform a wide range of functions in tight spaces. However, despite their versatility, improper use can lead to costly mistakes, reduced machine efficiency, and even jobsite accidents. Understanding the common errors that operators make during mini excavator digging is vital to ensure productivity, safety, and machine longevity.
This blog aims to provide a detailed exploration of five major mistakes frequently encountered in mini excavator digging operations. Whether you’re a seasoned contractor or a novice operator, recognizing and avoiding these errors will lead to smoother project execution and reduced operational risks.
Minigraafmachine Digging Error #1: Incorrect Bucket Selection
Choosing the wrong bucket is more than a minor oversight—it can derail an entire excavation process. The variety of available bucket types can confuse even experienced operators, making it critical to understand the role of each. Trenching buckets, grading buckets, and tilting buckets each have specialized purposes.
For example, grading buckets offer wider coverage and are ideal for leveling tasks, while trenching buckets are narrow and designed for precision digging. A mismatch between bucket type and job requirements results in energy inefficiency, operator fatigue, and inconsistent trench profiles.
Additionally, poor bucket selection leads to accelerated wear on critical machine components. Overloading the hydraulics system by using a heavy-duty bucket in unsuitable conditions can compromise seals, rams, and joints. To avoid this, operators should consult load charts and manufacturer recommendations specific to their mini excavator model.
Don’t overlook the importance of the bucket’s wear components either. Teeth configuration—whether standard, tiger, or twin-tiger—impacts penetration and efficiency in materials like clay, gravel, or compacted soil. Replacing worn teeth before they become blunt ensures productivity remains high and strain on the arm is minimized.
Minigraafmachine Digging Error #2: Poor Ground Assessment
Failure to assess ground conditions can lead to more than poor results—it poses serious safety risks. Mini excavators, while nimble, are still vulnerable to shifting terrain, underground voids, or unexpected obstructions. Wet clay may behave entirely differently from dry sand, and only a careful assessment can inform proper adjustments to digging techniques.
Some of the consequences of poor ground assessment include:
- Trench collapse due to unstable soil walls
- Undetected utility lines, leading to costly and dangerous hits
- Machine bog-down, especially in soft or waterlogged soil
A proper ground evaluation involves more than just a quick glance. It may require soil testing, analysis of moisture content, and even bringing in ground-penetrating radar for utility detection in urban environments. In addition, slope gradients, rainfall forecasts, and nearby traffic patterns can influence equipment performance and stability.
An experienced foreman or supervisor should lead the site walk-through, marking digging zones, flagging potential hazards, and determining the most suitable excavation method. This initial preparation can save hours in the field and prevent expensive recovery efforts after mishaps.
Minigraafmachine Digging Error #3: Inadequate Machine Positioning
Proper positioning isn’t just about placing the machine close to the dig site—it’s a strategy that affects fuel usage, cycle time, and machine strain. Effective mini excavator digging depends heavily on stable, level placement. The boom and arm should be allowed to move in smooth arcs, maximizing breakout force and operator visibility.
Incorrect positioning may lead to:
- Lopsided trench profiles
- Overextension of the boom and stick
- Operator blind spots, increasing the risk of collision or trench wall failure
When working in confined urban zones or steep slopes, positioning becomes even more critical. The mini excavator should always be facing the direction of digging to allow natural arm articulation. The tracks should be aligned parallel to the excavation area, enabling efficient swinging and dumping without over-rotating the machine.
Moreover, the undercarriage must be stabilized before any digging begins. For rubber-tracked models, using the blade as an anchor can improve steadiness. Taking the time to align and stabilize the unit may seem tedious, but it dramatically improves digging precision and safety.
Minigraafmachine Digging Error #4: Overreliance on Full Power
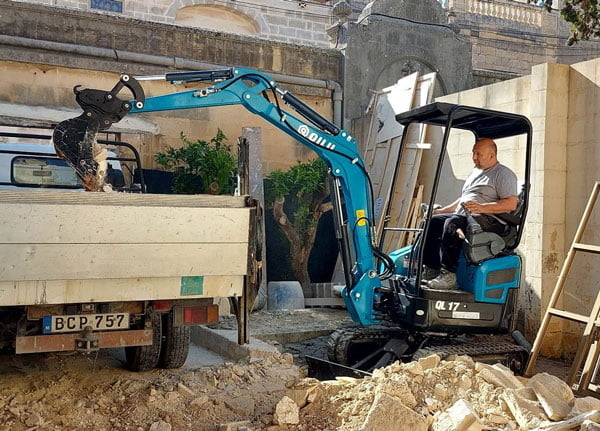
Full throttle may sound like the fast lane to productivity, but it’s often the fastest route to equipment damage. New operators frequently make the mistake of pushing the excavator’s limits continuously, leading to premature component failure.
High-pressure digging should be reserved for short bursts when encountering particularly stubborn materials. Otherwise, smooth, consistent operations using medium power settings will extend machine life and improve control. The real skill in mini excavator digging lies in modulation—not brute strength.
Signs you’re overusing power include:
- Jerky arm and bucket movements
- Hydraulic overheating
- Reduced fuel efficiency
- Choppy or uneven trenching
Modern mini excavators often come with multiple operating modes (eco, standard, high power). Selecting the appropriate mode based on workload and ground condition can improve both performance and fuel economy.
Minigraafmachine Digging Error #5: Neglecting Routine Maintenance
Maintenance is the heartbeat of machine reliability. Yet, it’s commonly ignored until a breakdown halts production. Mini excavator digging places constant stress on critical systems—tracks, hydraulics, pins, bushings, and cooling components are all vulnerable.
Neglect often results in:
- Hydraulic leaks
- Engine overheating
- Loose or broken bucket links
- Track misalignment and premature wear
Establishing a daily, weekly, and monthly maintenance schedule is essential. This includes:
- Checking and topping off fluids
- Inspecting hoses for wear or bulges
- Tightening bolts and fasteners
- Cleaning filters and intakes
- Lubricating pivot points
Preventative maintenance costs are a fraction of repair expenses. Moreover, machine downtime can impact project timelines and profitability. Maintaining detailed service logs also supports equipment resale value.
Additionally, it’s wise to train all operators in basic maintenance protocols. They’re the first line of defense in spotting abnormalities and can report issues before they escalate into major repairs.
Common Impacts of Minigraafmachine Digging Mistakes
To better understand the consequences of the mistakes outlined above, the table below compares key performance areas and the potential effects of improper practices.
Mini Excavator Digging Mistake | Consequences | Recommended Action |
---|---|---|
Incorrect Bucket Selection | Reduced efficiency, excessive wear | Choose bucket based on soil and trench size |
Poor Ground Assessment | Machine damage, safety hazards | Perform detailed site evaluation |
Inadequate Machine Positioning | Inaccuracy, tipping risk | Level and align before digging |
Overreliance on Full Power | Hydraulic stress, short lifespan | Use power selectively |
Neglecting Routine Maintenance | Unplanned downtime, operational delays | Follow maintenance schedules rigorously |
How to Improve Your Minigraafmachine Digging Technique
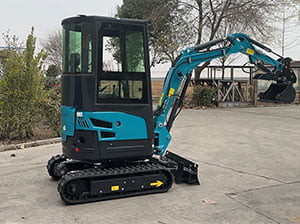
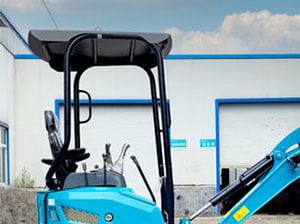
Improving your mini excavator digging technique involves more than avoiding mistakes. It requires a proactive approach to training, equipment knowledge, and site planning. Operators should receive proper certification and refresher courses periodically. Simulation-based training and practice sessions on various terrains help build adaptable skills.
Additionally, keeping up with equipment advancements can significantly enhance performance. Many modern mini excavators offer automation features, adjustable hydraulic settings, and digital controls that streamline digging. Embracing technology can reduce human error and boost productivity.
Communication is another vital element. Supervisors and team members must coordinate effectively to avoid errors in excavation planning, utility detection, and equipment deployment. Detailed project briefs and daily toolbox talks are simple yet effective strategies.
Conclusie
Minigraafmachine digging is a crucial task that demands precision, planning, and respect for equipment capabilities. The five critical errors—incorrect bucket selection, poor ground assessment, inadequate machine positioning, overuse of full power, and neglecting maintenance—can derail any project, regardless of its scale.
By recognizing and addressing these common pitfalls, operators and project managers can ensure safer worksites, enhanced productivity, and longer equipment lifespan. Success in mini excavator digging is less about working harder and more about working smarter. Avoid these mistakes, and your results will speak for themselves.
FAQ
What is the ideal bucket size for mini excavator digging?
The ideal bucket size depends on soil conditions, project dimensions, and the specific task. Typically, buckets range from 12 to 36 inches for mini excavators.
Can I use a minigraafmachine for rocky soil digging?
Yes, but it requires reinforced bucket teeth and slower digging speeds. Assess ground conditions beforehand to avoid equipment strain.
How often should I service my minigraafmachine?
Daily pre-use inspections are essential, with full maintenance checks recommended every 250 hours of operation or as per the manufacturer’s guidelines.
Is full power digging harmful for minigraafmachines?
Consistently using full power can wear out hydraulic systems and reduce machine life. Controlled, adaptive digging techniques are more effective.
What safety checks should I perform before minigraafmachine digging?
Inspect the bucket and arm, check fluid levels, test hydraulic functions, verify track tension, and ensure the machine is level and stable before operation.