Welkom op mijn blog!
Voordat we in de inhoud duiken, zou ik het leuk vinden als je me volgt op mijn sociale mediaplatforms waar ik meer inzichten deel, in contact kom met de community en updates plaats. Dit is hoe je met mij in contact kunt komen:
Facebook: https://www.facebook.com/profile.php?id=100072217509763
LinkedIn: https://www.linkedin.com/company/74949059/admin/dashboard/
YouTube:www.youtube.com/@tractormanufacturer-lc5qz,www.youtube.com/@excavatormanufacturers-sn9hk
TikTok: www.tiktok.com/@tractontwikkelaar, www.tiktok.com/@graafmachinefabrikanten
Laten we nu samen aan onze reis beginnen. Ik hoop dat je de inhoud hier inzichtelijk, boeiend en waardevol vindt.
Inhoudsopgave
Inleiding
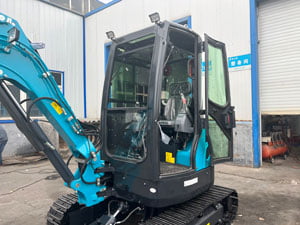
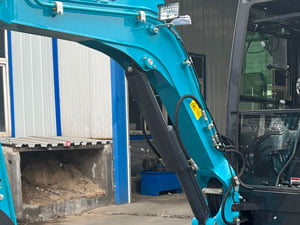
Excavators are among the most powerful and versatile machines used on construction sites, capable of handling a wide range of tasks, from digging trenches to lifting and transporting heavy materials. Their strength and adaptability make them essential for many construction, demolition, and mining projects. However, despite their usefulness, excavators pose several safety risks that must be carefully managed to ensure the well-being of operators and workers on site. Excavator safety is not just a regulatory requirement; it is a critical aspect of any construction project that directly impacts both the safety of personnel and the smooth execution of tasks.
Excavator safety hazards can arise from a variety of factors, including the operation of the machine itself, the surrounding environment, and even the behavior of other workers on the site. From tipping over to inadvertent collisions with workers, the risks associated with excavators are significant, which is why understanding and addressing these hazards is of utmost importance. Ensuring excavator safety on the jobsite requires a proactive approach, with operators and managers implementing strategies to minimize risk.
In this blog, we will explore the top six graafmachine safety hazards that every operator and construction manager should be aware of. We will also offer practical safety tips to mitigate these risks, providing you with valuable information to keep your jobsite safe. Whether you are an experienced operator or a manager overseeing excavation operations, understanding these potential hazards and how to prevent them is essential to maintaining a safe working environment. By adhering to proper excavator safety practices, you can avoid accidents, improve productivity, and ensure the overall safety of the jobsite.
Let’s dive into the critical elements of excavator safety and explore what you need to know to protect both yourself and those around you.
NO 1. Risk of Crushing and Pinching Injuries
One of the most significant safety hazards associated with excavators is the risk of crushing and pinching injuries. Excavators are equipped with large, powerful arms and buckets that, when not operated carefully, can cause serious harm to nearby workers. The sheer strength and size of these machines make them incredibly effective for digging, lifting, and moving heavy loads, but they also present considerable safety risks.
Pinching accidents typically occur when workers are caught between the machine’s moving parts, such as the bucket and the arm, or between the machine and obstacles on the ground, including other machinery or structures. The force exerted by an excavator’s hydraulic system can easily cause crushing injuries, making it a top concern in graafmachine safety.
To avoid crushing or pinching injuries, it’s crucial to maintain a safe distance from the excavator when it’s in operation. A key aspect of graafmachine safety is ensuring that workers are fully aware of the machine’s range of movement and the risks associated with being in close proximity to moving parts. Workers should always stay within the operator’s line of sight, which is critical for clear communication and reducing the risk of accidents. Excavator operators should use their mirrors, cameras, or spotters to ensure that no one is in the danger zone before moving or operating the machine.
In addition, ground personnel should be trained to recognize the potential hazards of working around an excavator. Clear protocols should be established for safe zones and movement around the machine, ensuring that workers avoid walking near moving parts or standing in areas where they might be at risk of being crushed. Proper use of signaling devices, such as whistles or two-way radios, can help alert workers when an excavator is about to perform a potentially hazardous movement.
Regular safety drills and refresher training for both operators and ground personnel are essential to reinforce the importance of safe practices. Providing all workers with a solid understanding of excavator safety guidelines and ensuring they are familiar with the machine’s limitations and potential risks can significantly reduce the occurrence of crushing and pinching injuries. Additionally, operators should regularly inspect their equipment for any signs of malfunction or wear, as these issues could increase the risk of an accident.
Ultimately, by emphasizing awareness, communication, and training, construction sites can create a safer environment that mitigates the risk of crushing or pinching injuries, ensuring both operator and worker safety when operating or working near excavators.
NO 2. Risk of Overturning or Tipping
Excavators, especially those operating on uneven or sloped surfaces, are at significant risk of overturning. This is one of the most dangerous safety hazards in the operation of these heavy machines. When the excavator’s center of gravity shifts too far, typically due to an unbalanced load, improper operation, or unstable ground conditions, the machine can tip over. This type of accident is particularly hazardous and can result in severe injuries or even fatalities. In fact, overturning is one of the leading causes of excavator-related fatalities, making it a critical concern in graafmachine safety.
To mitigate the risk of overturning, operators must prioritize maintaining the stability of the excavator at all times. Ensuring that the excavator is positioned on firm, level ground is one of the first steps in preventing this type of accident. Operators should always assess the ground conditions before starting any operation. If the surface is uneven, soft, or unstable, they should refrain from operating the excavator or use additional support measures, such as stabilizers or mats, to distribute the weight and provide a more secure base.
Load management plays a crucial role in preventing an excavator from tipping over. Graafmachine safety guidelines emphasize that operators should avoid overloading the machine, as an excessive load can shift the center of gravity, making the machine more prone to toppling. When lifting or digging, the load should be positioned as close to the center of the machine as possible. Operators should also be aware of the maximum lifting capacities for their specific model and avoid exceeding those limits. When lifting heavy loads, operators should never attempt to move the machine with an unbalanced load, as this increases the risk of tipping.
In addition to load management, operators should be trained in proper excavation techniques. Proper use of the excavator’s controls, combined with knowledge of the machine’s operating range and limits, is essential for graafmachine safety. Using the excavator’s built-in features, such as the level indicator or slope detector, can help operators maintain balance when working on uneven terrain. Regular training and retraining are vital to ensure that operators are aware of the risks associated with working on slopes or unstable ground, and are skilled in using the excavator safely.
Excavators should also undergo routine inspections and maintenance checks to ensure that all components, such as the hydraulic system and stabilizers, are functioning properly. Malfunctions or wear-and-tear issues, such as hydraulic leaks or worn-out stabilizers, can compromise the stability of the machine and increase the risk of an accident. Preventative maintenance is a key part of graafmachine safety, and operators should always ensure their equipment is in good working condition before operation.
Lastly, it is crucial to establish clear safety protocols for working around excavators, especially in situations where overturning could occur. This includes marking off safe zones, using spotters to guide the operator when working in confined or sloped areas, and enforcing strict no-go areas for ground personnel. By taking these precautions and fostering a strong culture of graafmachine safety, construction sites can significantly reduce the risk of overturning accidents and create a safer working environment for all.
Through vigilance, training, and adherence to safety guidelines, the likelihood of an excavator tipping over can be minimized, protecting both operators and other workers on the jobsite.
NO 3. Risk of Collisions and Strikes
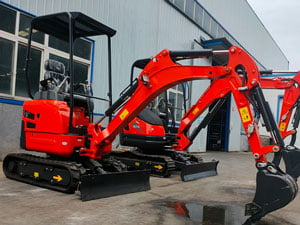
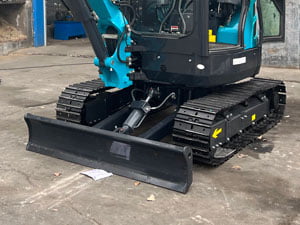
Excavators, particularly those working in confined spaces or near other machines, are at a heightened risk of collisions with other equipment, workers, or obstacles on the job site. These types of accidents can have catastrophic consequences, not only causing significant damage to equipment but also leading to severe injuries or fatalities. The risk of collisions is especially high when the operator cannot see the surroundings clearly—such as when operating the excavator with the arm extended or when working in reverse. In these situations, blind spots can prevent the operator from fully assessing the area around the machine, making graafmachine safety even more critical.
To mitigate the risk of collisions, one of the most effective strategies is ensuring that a spotter is present when the excavator is moving in tight spaces. A spotter can guide the operator by providing real-time feedback on the surroundings and alerting them to potential hazards. The spotter should be clearly visible to the operator at all times, and communication should be maintained through hand signals, radios, or other signaling devices. Graafmachine safety protocols recommend that the operator always follow the spotter’s guidance when working in constrained or high-risk areas. The spotter’s role is to assist in navigating tight spaces, such as near walls, other machinery, or personnel, while ensuring the excavator’s path remains clear.
In addition to the use of spotters, operators should always take the time to thoroughly check their surroundings before starting work. This includes scanning the area for potential hazards, such as workers, vehicles, or other equipment, and ensuring that no one is in the machine’s potential swing radius. A quick walk-around inspection of the machine should also be conducted to ensure that the area around the excavator is free from obstructions and that all equipment is in proper working order. Establishing a habit of pre-operation checks is an essential part of graafmachine safety.
Another way to enhance graafmachine safety and reduce blind spots is by utilizing safety features such as cameras, alarms, and sensors. Many modern excavators are equipped with rearview cameras, side cameras, or proximity sensors that can help the operator see blind spots that would otherwise be difficult to monitor. These technologies can provide a clearer view of the immediate surroundings, especially when working in reverse or in areas with limited visibility. Additionally, audible alarms, such as backup beepers, can alert workers on the ground when the excavator is in motion or when the machine is backing up. These alarms can serve as an early warning system, allowing workers to take appropriate action to avoid accidents.
To further improve graafmachine safety, it is crucial for all workers on the job site to be aware of the excavator’s movements. Establishing clear communication and ensuring that all personnel are trained in excavator safety procedures can significantly reduce the risk of collisions. Workers should be aware of the machine’s operating zones and avoid entering areas where the excavator is working. Construction sites should also be organized with clear traffic paths, and machinery should be positioned in a way that minimizes the risk of conflicts between different types of equipment.
Regular safety meetings and refresher training for both operators and ground personnel are vital to ensure that everyone understands the risks of working around excavators and knows how to reduce those risks. These training sessions should cover proper communication protocols, safe walking routes, and how to use safety features like cameras and alarms effectively.
By implementing these safety measures, construction sites can significantly reduce the likelihood of excavator collisions and create a safer working environment. A combination of good visibility, effective communication, proper use of technology, and thorough training are all crucial components of excavator safety that help to prevent accidents and keep workers safe from harm. With these steps in place, operators and ground personnel can work together to ensure that excavators can perform their tasks efficiently while minimizing the risk of collisions.
NO 4. Risk of Falling from the Excavator
Another hazard that is often overlooked on construction sites is the risk of falling from the excavator, especially when the operator or a worker is climbing in or out of the machine. Although this might seem like a minor issue compared to the heavy machinery’s main operational risks, falls can result in serious injuries, including broken bones, sprains, or even head trauma. Graafmachine safety protocols emphasize the importance of taking this risk seriously, as falls from excavators, especially from heights, are a leading cause of non-operator-related injuries on job sites.
To reduce this risk, operators should always use the machine’s handrails and steps when entering or exiting the cab. These features are designed to provide secure, stable points of contact, making it much safer to climb in or out of the excavator. Operators should be trained to always use both hands when climbing and ensure that their footing is secure on the steps. It’s important to remember that the handrails and steps are part of the graafmachine safety design and are essential for minimizing the risk of falling.
Jumping or skipping steps can be tempting, especially when workers are in a rush or distracted, but it significantly increases the risk of slips, trips, and falls. Excavator safety guidelines recommend that operators should avoid taking shortcuts, such as jumping down from the machine or climbing up without using the proper steps or handrails. This seemingly small action can lead to severe injuries. Even a short fall from a height can cause fractures or, in more extreme cases, traumatic head injuries.
Another important factor in preventing falls is ensuring that the ground surrounding the excavator is stable and level. Graafmachine safety standards call for operators to inspect the area before climbing on or off the machine. If the ground is soft, uneven, or cluttered with debris, it can increase the likelihood of slipping or losing balance. In such cases, the operator should take extra care when entering or exiting the cab, or ideally, wait for the ground to be cleared or made more stable. It’s also important that workers are aware of the surrounding environment, making sure that they are not stepping over hoses, cables, or other obstacles that could cause them to trip.
In addition to individual precautions, all personnel on the job site should be reminded of excavator safety measures related to entering and exiting the machine. Workers should avoid crowding around the excavator, especially when the operator is entering or exiting. A designated area should be established where workers can safely move around the excavator without interfering with the operator’s movements. For particularly high machines, or when working in environments where the ground is not stable, additional safety equipment such as harnesses or fall arrest systems might be warranted, although this is not always necessary for standard excavator operations.
Regular inspections of the excavator’s steps, handrails, and overall cab design are also an essential part of excavator safety. Over time, components such as handrails can become loose or damaged, which can increase the likelihood of an accident. A proactive approach to maintenance, including ensuring that the steps and handrails are in good condition, can significantly reduce the risks associated with falls.
Finally, it is essential to conduct regular safety briefings and provide workers with training focused on safe entry and exit techniques. Training should include demonstrating the correct use of the handrails and steps, as well as discussing the potential hazards of improper entry and exit. Encouraging a culture of excavator safety, where all workers understand the importance of following safe practices, can lead to a substantial reduction in fall-related injuries.
In summary, while it might seem like a small issue compared to the larger operational hazards, falling from an excavator can lead to severe injuries that are entirely preventable. By using the proper steps and handrails, avoiding shortcuts, checking the stability of the ground, and promoting awareness on the job site, both operators and ground personnel can significantly reduce the risk of falls. Prioritizing excavator safety in all aspects of machine operation ensures a safer, more efficient work environment for everyone involved.
NO 5. Risk of Mechanical Failure
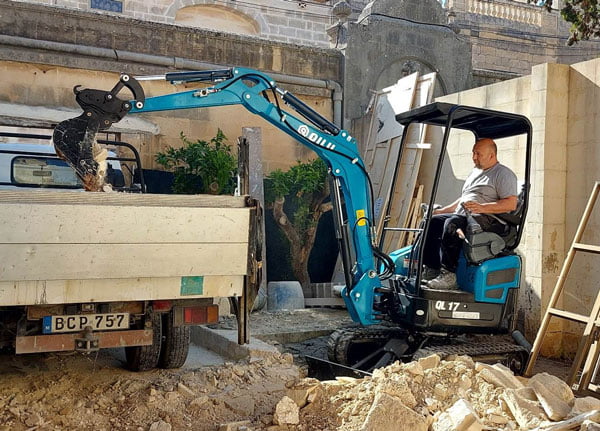
Mechanical failure is another significant risk in graafmachine safety that cannot be overlooked. Excavators, like any complex piece of machinery, rely on various systems, including the hydraulic system, engine, and other critical components, to function smoothly. A malfunction in any of these systems can lead to a sudden loss of control, causing both damage to the machine and potential injury to the operator or surrounding workers. These failures can be particularly dangerous because they often occur without warning, leading to accidents that could have been avoided with proper attention and care. As part of excavator safety best practices, regular maintenance and thorough inspections are essential to reduce the likelihood of mechanical failures.
To minimize the risk of mechanical failure, operators should conduct daily pre-operation checks to ensure that the excavator is in good working condition. These checks should be considered a fundamental part of excavator safety procedures and performed before every shift. A pre-operation inspection typically involves checking the machine’s key components, such as the hydraulic system, engine, brakes, and electrical system, to ensure they are functioning properly.
Operators should inspect hoses and lines for any signs of wear or leaks, check the fluid levels (oil, hydraulic fluid, coolant), and verify that all moving parts are in good condition and properly lubricated. Catching issues early during these routine checks can prevent more serious problems from arising during operation, which in turn reduces the risk of mechanical failure.
In addition to these daily checks, operators should also be trained to identify warning signs of potential mechanical issues that might arise while the machine is in use. These signs include unusual noises (like grinding or hissing), irregular machine performance (such as jerky or sluggish movements), or visible fluid leaks. If any of these signs are detected, operators should immediately stop the machine and perform a more detailed inspection.
Excavator safety protocols emphasize that no machine should be operated if it shows any signs of malfunction or if the operator is unsure of its safety. A malfunction in a critical component such as the hydraulic system or engine can lead to a sudden and uncontrolled movement of the excavator, posing a severe risk to the operator and other workers.
Routine maintenance is another vital aspect of graafmachine safety that helps prevent mechanical failure. Scheduled maintenance should not be neglected, as it ensures that the machine is operating at peak efficiency and that any worn-out parts are replaced before they fail. Maintenance tasks such as checking and replacing filters, inspecting the undercarriage, and tightening bolts and fasteners help keep the excavator running smoothly. Regular maintenance also includes evaluating the condition of the machine’s electrical and hydraulic systems, as these are integral to the excavator’s performance. Failure to maintain these systems properly can lead to dangerous breakdowns.
Operators should also be encouraged to follow the manufacturer’s recommended service schedule for their specific model of excavator. These guidelines outline when and how certain components should be serviced or replaced, and adhering to these recommendations can significantly extend the life of the equipment. Additionally, proper record-keeping of maintenance and repairs is an essential practice for tracking the condition of the excavator and identifying potential issues before they lead to mechanical failures.
An important part of graafmachine safety is also educating operators and maintenance personnel about the importance of proper lubrication. Lack of lubrication can lead to friction, excessive wear, and ultimately the failure of critical moving parts. Ensuring that all joints, hydraulic components, and mechanical linkages are adequately lubricated reduces wear and tear, minimizes breakdowns, and enhances the overall longevity of the machine.
Furthermore, it’s essential for operators to be vigilant and mindful of how they operate the excavator. Overloading the machine or using it beyond its capacity can put unnecessary strain on the engine and hydraulic system, leading to mechanical failure. Operators should always adhere to the excavator’s load limits and avoid pushing the machine past its designed capabilities. Safe operating practices, such as avoiding sudden jerky movements and minimizing rapid acceleration or deceleration, can also reduce stress on the machine and prevent wear that might lead to malfunctions.
In summary, mechanical failure is a significant risk in excavator safety, but it can be effectively mitigated through regular maintenance, thorough inspections, and operator vigilance. By conducting daily pre-operation checks, addressing warning signs promptly, adhering to routine maintenance schedules, and following best operational practices, the likelihood of a mechanical failure occurring is greatly reduced. Ultimately, a proactive approach to graafmachine safety ensures that the equipment remains in good working order, protecting both the operator and workers on site from the dangers associated with mechanical malfunctions.
NO 6. Risk of Excavator Safety Hazards from Weather Conditions
Weather conditions can have a significant impact on excavator safety, as they directly affect the stability and control of the machine. Extreme weather, such as heavy rain, snow, high winds, or extreme temperatures, can create dangerous working conditions that compromise both the operator’s safety and the machine’s performance. Wet or icy surfaces, for example, can increase the risk of the excavator slipping, especially when the machine is on an incline or navigating uneven ground. On the other hand, strong winds can make it difficult for the operator to maintain control, particularly when lifting or moving heavy loads. Graafmachine safety becomes even more critical under these conditions, as the risk of accidents or equipment damage increases significantly.
To mitigate these risks, operators must be proactive in monitoring weather conditions regularly. Weather forecasts and updates should be checked before starting the workday and throughout the day, especially if conditions are forecasted to worsen. By being aware of the changing weather, operators can plan their tasks more effectively and adjust their work practices accordingly. For example, if heavy rain is expected, operators may decide to complete tasks that are less affected by wet conditions, such as site preparation, while postponing tasks that require precise control or movement of heavy loads.
One of the most important steps in excavator safety when working in adverse weather is to stop operating the machine if conditions become too hazardous. If thunderstorms are approaching, or extreme winds are forecast, it is critical that the operator ceases work immediately and seeks shelter in a safe area. Lightning, in particular, poses a significant risk on construction sites, as it can cause not only electrical failures but also fires and other damage. High winds, especially when combined with the movement of heavy loads, can destabilize the machine and make it nearly impossible to control. In such conditions, it is always safer to stop work until conditions improve.
In addition to stopping work in extreme conditions, extra precautions should be taken when working in wet or icy conditions. These conditions increase the risk of the excavator sliding, tipping over, or losing traction, particularly if the machine is operating on steep or uneven ground. To reduce the risk of slipping, operators should reduce speed, avoid sharp turns, and exercise extreme caution when lifting or moving heavy loads. Sudden movements, such as jerking the controls or attempting to lift a load too quickly, can cause the machine to lose balance or traction. A gradual and controlled approach is essential for maintaining stability during these conditions.
When the ground is wet or icy, it may also be necessary to adjust the machine’s configuration to improve stability. For example, in icy conditions, operators should ensure that the excavator is equipped with appropriate tires or tracks that provide better grip. If the ground is particularly soft or slippery, additional precautions, such as placing mats or boards underneath the machine’s tracks, can provide added support and prevent the excavator from sinking or slipping.
In cold weather, operators should also be mindful of how the low temperatures can affect the machine’s performance. Cold temperatures can cause hydraulic fluids and engine oils to thicken, leading to reduced efficiency and potential damage. It’s important to allow the excavator to warm up properly before use and to ensure that all fluids are at the correct levels and viscosities for the temperature. This also includes checking the battery, as cold weather can cause batteries to drain more quickly, which could lead to starting problems or electrical failures.
The operator’s safety gear should also be considered when working in extreme weather. In cold temperatures or snow, wearing insulated clothing, gloves, and boots is essential to avoid frostbite or hypothermia. Similarly, in hot weather, operators should stay hydrated, wear breathable clothing, and take breaks in shaded areas to prevent heat exhaustion.
Finally, it’s important to keep in mind that the weather can change rapidly, especially in certain regions where storms can develop without much warning. This means that even if the weather starts out favorable, operators and construction managers must be prepared to stop work quickly and safely if conditions deteriorate. A clear safety plan, including communication protocols and procedures for halting operations in dangerous weather, is essential for ensuring that graafmachine safety is maintained under all circumstances.
In summary, weather conditions play a significant role in excavator safety and must always be factored into the operator’s decision-making process. By monitoring the weather, adjusting work practices, and taking extra precautions when conditions become hazardous, operators can reduce the risks associated with adverse weather and ensure a safer working environment for everyone on site. Staying vigilant and prepared for changing weather can help prevent accidents and ensure that the excavator is used safely and effectively, regardless of the conditions.
Table: Key Excavator Safety Risks and Preventive Measures
Safety Hazard | Preventive Measures |
---|---|
Crushing and Pinching Injuries | Maintain a safe distance from the machine, train workers to stay in the operator’s line of sight, and use safety barriers when needed. |
Overturning or Tipping | Ensure stable ground, avoid overloading, use a level indicator, and train operators on proper operation techniques. |
Collisions and Strikes | Use spotters in confined spaces, check surroundings before operation, and use cameras or alarms to reduce blind spots. |
Falling from the Excavator | Always use handrails and steps, avoid jumping or shortcuts, and check the stability of the ground before entering or exiting. |
Mechanical Failure | Conduct daily pre-operation checks, maintain equipment regularly, and train operators to spot signs of mechanical issues. |
Weather Conditions | Monitor weather regularly, halt work during hazardous conditions, and adjust operations for wet or icy surfaces. |
Conclusie
Excavator safety is a vital aspect of construction and excavation operations, and being aware of the potential hazards is crucial for minimizing risks. By understanding and addressing the six primary excavator safety hazards—crushing, overturning, collisions, falling, mechanical failure, and weather conditions—operators and workers can significantly reduce the chance of accidents on the job site. Proper training, daily maintenance checks, and adherence to safety protocols are essential in ensuring a safe work environment for everyone involved.
FAQ
Q1: How can I prevent graafmachine tipping on uneven ground?
A1: To prevent tipping, ensure that the ground is firm and stable before starting operations. Avoid operating the excavator on sloped surfaces and manage loads carefully. Using the machine’s level indicator can also help maintain balance.
Q2: What should I do if I notice mechanical issues with my excavator?
A2: If you notice any mechanical issues, immediately stop operating the excavator and report the problem to your maintenance team. Perform daily checks to identify potential issues early, and ensure regular maintenance is carried out to keep the machine in good working condition.
Q3: Can weather conditions affect graafmachine safety?
A3: Yes, weather conditions like heavy rain, snow, or high winds can increase the risk of accidents. Always monitor the weather and stop working if conditions become too hazardous. Adjust your operations to suit the weather, especially in wet or icy conditions.