Welkom op mijn blog!
Ik ben blij dat je er bent! Voordat we in de inhoud duiken, zou ik het leuk vinden als je me volgt op mijn social media platforms. Hier deel ik extra inzichten, ga ik de dialoog aan met een geweldige community en houd ik je op de hoogte van het laatste nieuws. Dit is hoe je op de hoogte kunt blijven:
Facebook: Connect met mij op Facebook
LinkedIn: Volg me op LinkedIn
▶️ YouTube: Kanaal trekkerfabrikant,Graafmachine fabrikanten kanaal
TikTok: Tractor Fabrikant,Graafmachine Fabrikant
Laten we nu samen aan deze reis beginnen! Ik hoop dat je de inhoud hier inzichtelijk, boeiend en vooral waardevol vindt. Laten we ontdekken, leren en groeien!
Inhoudsopgave
Inleiding
Minigraafmachines are known for their versatility and ability to operate in tight spaces, making them indispensable for construction, landscaping, and utility projects. One crucial yet often overlooked component of these machines is the tracks. Choosing the right tracks for mini excavator operations can significantly enhance performance, improve safety, and extend the machine’s lifespan.
Whether you use your mini excavator daily or occasionally, investing in the most suitable tracks is essential to avoid unnecessary downtime and excessive wear. In this blog, we will explore the three essential tracks for mini excavator work, diving deep into their features, benefits, and suitable applications. By the end, you’ll have a clear understanding of what to look for in high-performance tracks for mini excavator usage.
Rubber Tracks for Minigraafmachine: A Flexible Solution
Rubber tracks are among the most popular options for mini excavators due to their versatility and operator comfort. These tracks are ideal for working on urban job sites, residential areas, and delicate surfaces where minimizing ground damage is critical.
Advantages of Rubber Tracks
- Oppervlaktebescherming: Rubber tracks minimize surface damage on pavements, lawns, and finished landscapes.
- Noise Reduction: They produce less noise compared to steel tracks, making them suitable for noise-sensitive areas.
- Comfort voor de operator: The rubber composition helps absorb vibration, enhancing comfort and reducing operator fatigue.
Best Use Cases for Rubber Tracks
Rubber tracks for mini excavator use are especially suitable for:
- Landscaping and gardening
- Indoor or urban demolition
- Utility work in residential neighborhoods
However, these tracks may wear faster on rough or abrasive terrain. Therefore, they are not recommended for projects that involve heavy-duty or rocky surfaces.
Steel Tracks for Minigraafmachine: Maximum Durability
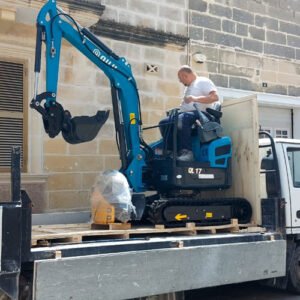
When durability and strength are the primary requirements, steel tracks are the go-to option. Designed for extreme environments, these tracks provide superior traction and resistance to wear.
Advantages of Steel Tracks
- Superior Traction: Steel tracks offer excellent grip on uneven and rocky surfaces.
- Long Lifespan: With proper maintenance, they can outlast rubber tracks significantly.
- Heavy-Duty Performance: Ideal for tasks involving heavy loads or large-scale excavation.
When to Use Steel Tracks
Tracks for mini excavator work made of steel are best suited for:
- Forestry and logging
- Quarry and mining operations
- Deep excavation and trenching in rocky soil
Steel tracks are less forgiving on finished surfaces and generate more noise, so they are typically used in industrial and rural environments where ground impact is not a concern.
Hybrid Tracks for Minigraafmachine: The Best of Both Worlds
Hybrid tracks combine the strength of steel with the surface protection of rubber. These tracks are gaining popularity for their ability to provide both durability and flexibility.
Advantages of Hybrid Tracks
- Balanced Performance: Offers durability without compromising surface integrity.
- Veelzijdigheid: Suitable for multiple terrain types, from concrete to dirt.
- Kosteneffectief: Often more affordable than high-end rubber or steel tracks over time due to reduced wear.
Ideal Applications for Hybrid Tracks
Hybrid tracks for mini excavator use are optimal for:
- Contractors working on varied terrain
- Municipal construction projects
- Mid-size excavation sites
They strike a good balance between comfort, longevity, and adaptability, making them an excellent choice for contractors handling diverse job site conditions.
Comparison Table: Essential Tracks for Minigraafmachine Work
Type spoor | Surface Impact | Duurzaamheid | Geluidsniveau | Beste voor |
---|---|---|---|---|
Rubber | Laag | Matig | Laag | Landscaping, residential areas |
Staal | Hoog | Hoog | Hoog | Mining, forestry, rocky terrain |
Hybride | Medium | Hoog | Medium | Mixed terrain, urban construction |
Key Considerations When Choosing Tracks for Minigraafmachine Work
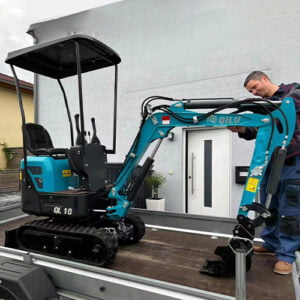
Choosing the correct tracks for mini excavator tasks isn’t simply a matter of selecting a material. A thoughtful evaluation of your job requirements, environment, and machine specifications will help you avoid inefficiencies and unnecessary costs.
Ground Conditions and Terrain Types
Ground conditions vary greatly between job sites, and each type of track performs differently based on the surface it operates on. For example, if you’re working on soft soil, grassy terrain, or finished surfaces such as asphalt and concrete, rubber tracks are generally preferable. They cause minimal damage and offer sufficient traction without compromising surface aesthetics.
For harsher environments—rocky ground, gravel pits, or undeveloped land—steel tracks shine. They bite into the terrain and provide a firm grip even on loose or uneven surfaces. Hybrid tracks offer moderate ground protection and can transition between hard and soft surfaces, making them valuable for contractors who manage multiple types of job sites.
Frequency of Use and Job Demands
The type and intensity of work you do should heavily influence your track choice. If you use your mini excavator daily under high-stress conditions—such as digging, trenching, or demolition—steel tracks or durable hybrid tracks may be more cost-effective over time. They are built to handle substantial wear and tear.
On the other hand, if you’re an occasional user or run your machine in controlled environments, rubber tracks provide adequate performance without the premium cost associated with heavy-duty solutions.
Budget, ROI, and Lifecycle Costs
While initial purchase price is an important factor, evaluating total lifecycle cost is even more critical. Rubber tracks may be cheaper to purchase but might require more frequent replacement depending on your work conditions. Steel and hybrid tracks, though more expensive upfront, often pay for themselves through extended lifespan and reduced downtime.
Machine Compatibility and OEM Specifications
Tracks for minigraafmachine use must match the specifications provided by the machine manufacturer. Track width, pitch, and sprocket compatibility directly impact the excavator’s stability, efficiency, and safety. Using incompatible tracks can cause serious mechanical issues or void warranties, making it vital to consult the OEM manual or a trusted technician before purchasing.
Environmental and Regulatory Constraints
Some job sites, especially in urban zones or protected areas, may enforce strict guidelines concerning ground disruption and noise levels. Rubber tracks are typically favored in such environments due to their quiet operation and minimal surface damage.
Parts Availability and Track Replacement Support
In regions where certain types of tracks are hard to find or take longer to ship, choosing a commonly available option may save you weeks of downtime. Be sure to check with suppliers and consider stocking extra track parts, especially if your excavator is mission-critical to ongoing operations.
Maintenance Tips for Tracks for Minigraafmachine Levensduur
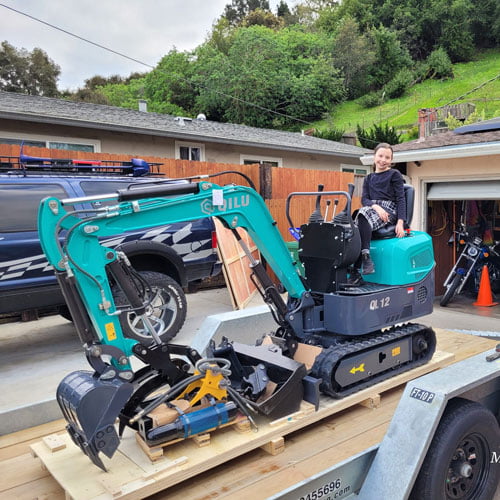
Proper maintenance of your tracks can significantly extend their lifespan and keep your mini excavator running efficiently.
Daily Inspection
Check for signs of wear, cracks, or misalignment. Address issues early to avoid expensive repairs.
Proper Tensioning
Incorrect track tension can accelerate wear. Follow your machine manufacturer’s recommendations for proper tension levels.
Cleaning After Use
Remove dirt, debris, and other materials from the tracks and undercarriage to prevent buildup and corrosion.
Scheduled Servicing
Regular maintenance by professionals ensures that tracks remain in optimal condition and reduces the risk of unexpected downtime.
Conclusie
Choosing the correct tracks for mini excavator operations is a strategic decision that can greatly impact productivity, machine longevity, and safety. Rubber tracks offer flexibility and surface protection, steel tracks provide unmatched durability for tough conditions, and hybrid tracks strike a balance ideal for varied environments.
By understanding the strengths and limitations of each type, contractors and equipment operators can make informed decisions that lead to better job outcomes and lower total ownership costs.
Investing in the right tracks for mini excavator use ensures your equipment remains a reliable partner on every project, whether you’re digging trenches in rocky soil or landscaping in a residential backyard.
FAQ
What are the most durable tracks for minigraafmachine use?
Steel tracks are typically the most durable, especially in extreme environments like quarries and forests.
Can I switch between rubber and steel tracks on the same minigraafmachine?
Yes, if your machine is designed for track interchangeability. Always check the manufacturer’s guidelines before switching.
Are hybrid tracks worth the investment?
Hybrid tracks offer a good balance of durability and versatility, making them ideal for operators working across varied terrain.
How often should I replace tracks for minigraafmachine use?
Track lifespan depends on usage and maintenance. Rubber tracks may last 1,200–1,600 hours, while steel tracks can last longer with proper care.
Do different tracks affect fuel efficiency?
Yes. Properly chosen and maintained tracks reduce rolling resistance and increase fuel efficiency, saving operational costs in the long run.