Welcome to My Blog!
Before we dive into the content, I’d love for you to join me on my social media platforms where I share more insights, engage with the community, and post updates. Here’s how you can connect with me:
Facebook: https://www.facebook.com/profile.php?id=100072217509763
LinkedIn: https://www.linkedin.com/company/74949059/admin/dashboard/
YouTube:www.youtube.com/@tractormanufacturer-lc5qz,www.youtube.com/@excavatormanufacturers-sn9hk
TikTok: www.tiktok.com/@tractormanufacturer, www.tiktok.com/@excavatormanufacturers
Now, let’s get started on our journey together. I hope you find the content here insightful, engaging, and valuable.
Table of Contents
Introduction
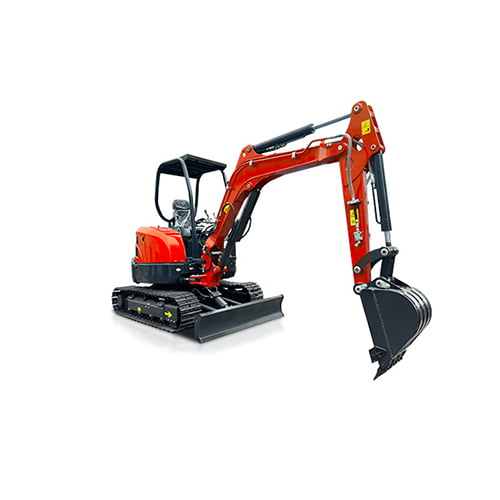
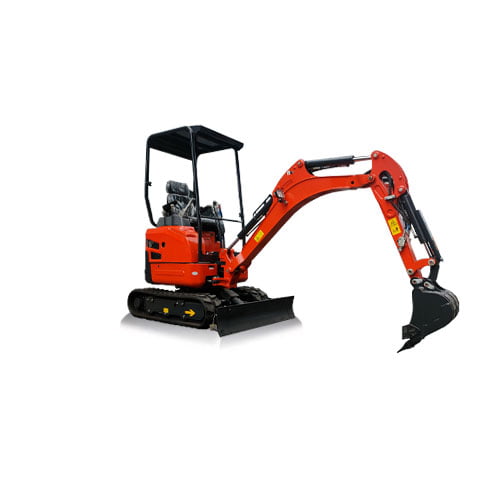
Excavators are essential for construction, mining, and many other industrial operations. However, excavator costs can quickly escalate if not carefully monitored. From operational inefficiencies to poor planning, several factors contribute to higher expenses. This article explores seven warning signs that indicate you might be overspending on excavator costs and provides actionable strategies to bring them under control.
By understanding these common pitfalls, businesses can reduce unnecessary expenses, improve productivity, and maximize the value of their equipment investments.
NO 1. Frequent Maintenance and Repairs
One of the most common signs of overspending is frequent maintenance or repair work on your excavators. While regular servicing is necessary to keep the equipment in optimal condition, repeated breakdowns and part replacements can drain your budget.
Causes of excessive maintenance costs include poor operator handling, low-quality spare parts, or aging equipment. If you notice recurring issues with specific components, it may indicate that the equipment is outdated or being misused.
Strategies to address frequent maintenance costs:
- Implement a preventative maintenance schedule to catch minor issues before they escalate.
- Conduct regular inspections to identify wear and tear early.
- Upgrade to newer models if repair costs outweigh the value of keeping older equipment operational.
Investing in high-quality parts and skilled technicians may initially seem costly but can significantly reduce long-term excavator costs.
NO 2. High Fuel Consumption
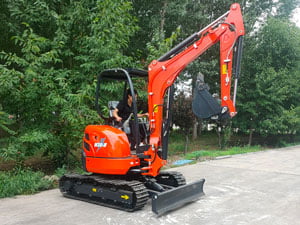
Fuel consumption is a major contributor to overall excavator costs, especially for machines that run for extended periods. If you notice your equipment consuming more fuel than expected, it may indicate issues like improper engine calibration, inefficient operating practices, or outdated machinery.
Modern excavators are designed to be fuel-efficient and environmentally friendly. Upgrading to newer models or implementing training programs for operators can reduce fuel consumption significantly.
Steps to reduce fuel costs:
- Monitor fuel usage daily to detect anomalies.
- Optimize job site workflows to minimize idling time.
- Train operators to use eco-friendly techniques, such as avoiding sudden acceleration.
NO 3. Over-Reliance on Rental Excavators
Renting excavators for short-term projects can be cost-effective, but over-reliance on rental equipment for long-term needs often leads to inflated excavator costs. Rental fees can add up quickly, particularly if you need the equipment for months or even years.
How to evaluate rental costs versus ownership:
- Calculate the total cost of renting over an extended period and compare it to purchase or lease options.
- Assess whether your projects require specific types of excavators consistently.
- Consider financing options if purchasing outright is not feasible.
Owning your equipment provides more control over maintenance schedules and eliminates recurring rental fees, which can save your business significant amounts over time.
NO 4. Ineffective Operator Training
Untrained operators can unintentionally cause damage to equipment, leading to higher repair and maintenance expenses. Improper handling may also result in poor fuel efficiency and increased wear and tear on the machine.
Why training matters for cost control:
- Skilled operators can use the equipment more efficiently, maximizing its lifespan.
- Proper training reduces the likelihood of accidents, minimizing downtime and liability costs.
Investing in regular training programs and certifications ensures that operators are knowledgeable about best practices, including efficient operation and basic maintenance tasks.
NO 5. Low Utilization Rates

Low utilization rates are another clear indicator of overspending on excavator costs. Paying for equipment that sits idle for extended periods represents wasted potential and unnecessary expenses.
How to improve utilization rates:
- Schedule equipment use more effectively by coordinating with project timelines.
- Rent out idle excavators to other contractors or projects.
- Use tracking software to monitor equipment usage and adjust accordingly.
Improving utilization rates ensures you’re getting maximum value from your investment, helping to offset the initial purchase or rental costs.
NO 6. Ignoring Technological Innovations
Incorporating new technologies into your operations can drastically reduce excavator costs. Features like GPS tracking, telematics, and automated systems improve operational efficiency and provide real-time data on fuel usage, maintenance needs, and operator performance.
Examples of cost-saving technologies:
- GPS systems help optimize excavation accuracy, reducing wasted time and resources.
- Telematics provide detailed reports on equipment health and usage patterns.
- Hybrid or electric excavators offer significant fuel savings over traditional models.
Ignoring these advancements means missing out on potential savings and operational improvements.
NO 7. Poor Budgeting and Cost Analysis
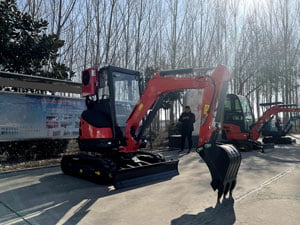
One of the most overlooked factors in escalating excavator costs is the lack of detailed budgeting and cost analysis. Without clear records of spending, it’s easy to lose track of expenses related to fuel, repairs, and operator wages.
Steps to implement better cost tracking:
- Use construction management software to monitor all aspects of equipment spending.
- Regularly review expense reports and identify areas for improvement.
- Set clear budgets for each project and ensure accountability.
By maintaining a clear overview of your costs, you can identify inefficiencies and adjust your strategies accordingly.
A Table to Compare Excavator Cost Contributors
The table below summarizes the key contributors to high excavator costs and potential mitigation strategies:
Cost Factor | Impact on Expenses | Mitigation Strategies |
---|---|---|
Maintenance and Repairs | Increases downtime and expenses | Schedule preventative maintenance |
Fuel Consumption | Major contributor to operating costs | Train operators and upgrade to efficient models |
Rental vs. Ownership | Long-term rental fees accumulate | Evaluate lease or purchase options |
Operator Training | Causes equipment misuse and damage | Provide regular training and certifications |
Idle Equipment | Wasted investment | Rent or sell underutilized machines |
Technology Gaps | Reduces operational efficiency | Adopt advanced tracking and automation tools |
Poor Budgeting | Leads to uncontrolled expenses | Implement cost tracking and detailed budgets |
Conclusion
Overspending on excavator costs is often the result of inefficiencies, outdated practices, or lack of planning. By addressing the seven warning signs outlined in this article, businesses can significantly reduce expenses, improve productivity, and get more value from their equipment investments.
Proactive measures like adopting technology, implementing better training programs, and maintaining clear records are key to controlling costs in the long term. Regular evaluations of your equipment’s performance and spending patterns will ensure that you stay within budget and maximize profitability.
FAQ
What is the most effective way to reduce fuel costs for excavators?
Reducing fuel costs for excavators requires a combination of strategies. One effective method is optimizing operator practices. Proper training can help operators avoid unnecessary idling, excessive engine revving, and inefficient digging techniques that consume more fuel. Another approach is upgrading to newer, fuel-efficient excavator models that incorporate advanced engine technologies, such as hybrid systems or low-emission engines. Additionally, maintaining proper tire pressure, using the right type of fuel, and ensuring regular servicing of the excavator’s engine can further enhance fuel economy.
How can I decide between renting and buying an excavator?
Consider the duration and frequency of use. Long-term projects typically make ownership more economical, while short-term needs are better suited for rentals.
Is investing in operator training worth the cost?
Absolutely, investing in operator training is a wise decision that yields significant savings and benefits. Skilled operators are less likely to cause avoidable wear and tear, reducing the frequency and expense of repairs. They are also more efficient in their operations, completing tasks in less time and with less fuel consumption. This not only lowers operational costs but also extends the excavator’s lifespan. Moreover, safety improves with proper training, decreasing the likelihood of accidents that could lead to costly downtime and liability issues.
What role does technology play in reducing excavator costs?
Technology plays an increasingly vital role in cost reduction for excavators. Tools like GPS and telematics systems enable precise digging and optimized route planning, minimizing unnecessary movement and fuel consumption. Telematics can also provide real-time data on equipment performance, alerting you to maintenance needs before issues escalate into costly breakdowns. Automation and smart controls in modern excavators improve operational accuracy, reducing material wastage. Additionally, predictive maintenance software can analyze usage patterns and recommend timely servicing, ensuring the machine operates at peak efficiency.
How often should excavators undergo maintenance?
Excavators should undergo preventative maintenance regularly, as outlined in the manufacturer’s guidelines. The frequency often depends on usage intensity, operating conditions, and machine type. Daily checks, such as inspecting fluids, tracks, and attachments, help identify minor issues early. For moderate use, a detailed servicing might be required every 250 to 500 hours of operation, while heavy-duty usage may necessitate more frequent attention. Regular maintenance includes tasks like oil changes, filter replacements, and hydraulic system inspections. Keeping to a strict maintenance schedule prevents unexpected breakdowns, extends equipment lifespan, and reduces overall costs.